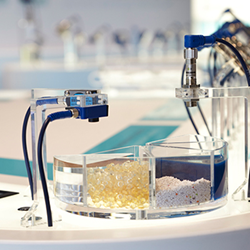
Troy, Michigan (PRWEB) September 09, 2014
The demands placed by industry on sensors and their companies are developing continuously – and ultrasound technology gives options to meet these demands, for virtually each conceivable application. As a leading manufacturer of ultrasonic sensor technologies, and with patents pending on a quantity of specific developments, this article appears at how challenging applications can be solved by microsonic’s business-top ultrasonic sensor technologies.

The trend towards miniaturisation while delivering maximum sensor overall performance indicates fantastic expectations are being placed on ultrasonic sensor companies. Microsonic has risen to the challenge of manufacturing sensors to meet and exceed these demands. microsonic, the ultrasonic sensor specialist, has just launched its new nano class developing on the proven efficiency of their compact class. The new nano is the shortest M12 ultrasonic sensor on the market.

What is reflected is also detected! 
In comparison to optical sensors (which detect light-reflecting/light-impenetrable objects) or inductive 
sensors (which recognise only ferromagnetic metal components), ultrasonic sensors can be applied to applications with practically no restrictions. Ultrasonic sensors detect nearly all sonically reflective supplies with out speak to and can be employed with nearly every fluid, gas, film, material or coarse-grained parts, chippings, fine sand as well as the thinnest of cables. These sensors provide higher measurement-precision in ranges of up to 15m. Even in dirty environments exactly where sensors are topic to particulate matter in the air and disruptive extraneous light, ultrasonic sensors can detect the intended object. Sound-absorbent objects can be detected with a two-way ultrasonic barrier, utilizing a fixed reflector.

The high sensitivity of the Nano ultrasonic sensor will enable for detection and measurement of virtually every conceivable material and its robust building makes these ultra-compact, ultrasonic sensors the best sensor for virtually each industrial application.

How do ultrasonic sensors function?
1. The normal ultrasound measurement principle, Echo Runtime Measurement, is applied in ultrasonic distance sensors and ultrasonic proximity switches for presence detection and distance measurement. An ultrasonic sensor emits a cyclical higher-frequency acoustic pulse which transmits by means of the air at the speed of sound. When it meets an object, it is reflected and the echo returns to the sensor. The interval among the emission of the ultrasound and the reception of the echo, is used to calculate the distance to or presence of the object.

2. Some applications require specific measurement strategies such as amplitude evaluation. Throughout ultrasonic sampling, the strength with which the signal is received provides details about the position or composition of the material, located amongst the sender and receiver. These measurement methods are utilized for applications such as double-sheet manage, label and splice applications or in web edge monitoring.

Examples for the industrial application of compact ultrasonic distance sensors:

The positioning of wafers in the semi-conductor market
Fill-level measurement in little containers
Wire-break monitoring
Sampling of little bottles in the packaging business
Presence checking
Detection of PCBs in the electronics business
Detection of stoppers in bottles
Detection of packaging
The monitoring of moistening agents in printing machines
The counting of tiny objects on the conveyor belt
Sheet detection on paper-processing machines
Detection of glass panes
Micro crack checks in the textile sector
Volume flow control for bulk material
Loop control 
Robot gripper arm positioning
Diameter measurement of modest coils
… and even more intelligence with the IO-Link
microsonic ultrasonic sensors serve all conventional interfaces, such as the interface of the future: IO-Hyperlink. The IO-Link interface enables the genuine-time, comprehensive and bi-directional transmission of measurement values, method information and service data among the control technique and the sensor. This technologies applied to sensors enables the simplification of commissioning, operation and maintenance of machines or systems the improvement of performance and availability the optimisation of process flows and the application of sensors in ever-a lot more application regions.

IO-Link connects the sensor with an IO-Hyperlink master via a normal 3-conductor sensor cable of up to 20 m in length. An IO-Link master is equipped with one particular or far more inputs and outputs to which an IO-Hyperlink device can be connected. Full compatibility with SIO mode (Regular IO mode) enables mixed operation. A number of sensors can be operated on a single master in IO-Hyperlink and SIO mode.

As an intelligent communications interface, IO-Hyperlink brings a number of advantages in comparison to other systems (such as the standard direct cabling) in terms of automation technologies, and will offer the base for revolutionary developments more than the coming years:

The 1st IO-Hyperlink capable sensor from microsonic was the pico+, ideally-suited to applications in the production of glass bottles, complete and empty crate manage or the sampling of empty PET bottles on a conveyor belt.

Here are some of the extra innovations obtainable from microsonic:

pico+ – compact form with 90° angular head, multiplex operation, IO-Hyperlink interface
pico+-ultrasonic sensors are a compact sensor with a M18 threaded physique and a housing length of only 41 mm. In addition to the axial beam direction, a housing variation is obtainable with a 90° angular head and radial beam direction for unique applications. With 4 detection ranges between 20 mm – 1.three m and 3 different output stages, the sensor family covers a broad spectrum of applications. Automatic synchronisation and multiplex operation enables the simultaneous operation of up to ten sensors in the most confined of spaces.

zws – rapidly measurements with higher machine speeds and in the smallest of gaps
With its detection range between 20 mm and 1 m and the switching and analogue outputs, the microsonic zws comes with a cuboid housing the type of the housing and its installation are compatible with a quantity of optical sensors. This facilitates the effortless changeover to ultrasonic sensors in vital applications. With a switching frequency of up to 250 Hz, the zws 7 is ideally suited for applications requiring quick sampling. With its optional “SoundPipe”, a waveguide attachment, it can also be utilized for specifically challenging measurement tasks such as counting at higher speeds and it can measure filling levels in the smallest of apertures – a typical application is the level measurement in microplate “wells” as employed in healthcare analysis applications.

sks – the highest of precision and an option to optical sensors 
The sks sensors had been previously the smallest ultrasonic sensors offered by microsonic and in comparison to the zws, present a 33 percent smaller housing volume. The sks is ideally suited for sampling printed circuit boards and wafers in the electronics industry or packaging machines on which transparent or hugely-reflective films need to have to be recognised. In addition to its very modest housing dimensions, with two M3 screw bushings for fastening, they have identical kind and match with a quantity of optical sensors they thus provide a true alternative for use in crucial applications. The sks measures with .1 mm resolution, thereby guaranteeing the highest of precision.

*New*: The Nano – The smallest ultrasonic sensor in the globe
With a total length of only 55 mm including connector, the new Nano from microsonic is the shortest M12 ultrasonic sensor offered on the market. The smallest of its sort in the planet, it offers two detection ranges: 250 and 350 mm, offered with analogue or switching output.

microsonic goods and options are obtainable in North America through TR Electronic

TR Electronic
customercare(at)trelectronic(dot)com
USA: 800-709-3300
CANADA: 800-265-9483





Associated Higher Precision Machining Press Releases