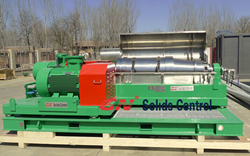
Houston,Texas (PRWEB) September 12, 2014
GN Solids America concentrate on the liquid and solids separation, recently, GN Solids America developed the new slurry separation plant for TBM drilling mud cleaning. It allows the contractor to get clean water from the TBM slurry for reuse in the TBM project. This saves a lot of income for the waste disposal expense. This plland also can recover drilling fluids for the drilling projects.

A tunnel boring machine (TBM) also known as a “mole”, is a machine utilised to excavate tunnels with a circular cross section through a range of soil and rock strata. TBM can bore via anything from tough rock to sand. Tunnel diameters can range from a metre (carried out with micro-TBMs) to 19.25 m to date. The TBM business use a similar technology like in the oil gas drilling. TBM utilize the drilling mud for the projects for cooling and sealing the hole. To recycle and reuse the drilling fluids, TBM requirements the slurry separation plant to clean the drilling fluids. Tunnels of significantly less than a meter or so in diameter are generally done using trenchless building methods or horizontal directional drilling rather than TBMs.

GN Solids Manage developed the TBM slurry separation program for contractors to get clean water for reuse in the TBM project.

Element 1) Main Slurry Separation Plant

The primary slurry separation plant is for separation solids upper of 45microns. GN primary slurry separation plant consist of following solids manage equipment.

1.1) Double Deck Shale Shaker
Model: GNZS706E-HB 
Vibrating mode: Linear Motion
Motor energy: 2×1.94 KW (Italy OLI, 2.5hp)
Vibrating strength: ≤7. G
Deck quantity: two
Screen location: Up deck: two.13 Square Meter, Reduce deck:2.63 Square Meter
Deck angle adjustment: Minus 1 Degree to 5 Degree.
Upper Screen Spec: 3x750x900mm with Opening 2mm
Bottom Screen Spec: 3x700x1250mm with Mesh API 40
Max Treating capacity: 300m³/h
Weight: 1742 kg
Dimension: 2717x2012x1413 mm
Feeding box type: Weir Back sort feeder

1.2 ) Desander Cleaner 
Model: GNZJ703E-3S 
Desander Cones: 10″x3ea 
Max Capacity 360m³/h 
Matching Shaker: GNZS703E 
Vibrating Mode: Linear Motion 
Motor Energy: 2×1.72kW(Italy Oli Brand Motor) 
Vibrating strength: ≤7. G 
Deck angle adjustment: Minus 1 Degree to 5 Degree. 
Screen region: 2.63 Square Meter 
Screen Specifications: three panels (750mm*1250mm API200) 
Starter magnetic force starter 
Weight: 1846Kg 
Dimension: 2419x2113x2147mm

Apart from the above two key solids handle equipment, there are mud tanks, centrifugal pumps, 
mud agitator as nicely a mud tank attachments for the primary slurry separation method.

Approach for the Major Slurry separation technique is as below:
The dirty slurry comes from the TBM and feeds to the GNZS706E-HB shale shaker leading layer screen for separation of solids larger than 2mm, and the fluids go by way of the top layer screen to the bottom layer screen to separate solids of 400 Microns.

Later on, a centrifugal pump takes fluid from the mud tank very first compartment to feed to the 3x10inch desander cones on the GNZJ703E-3S shale shaker. This is the third phase separation for solids larger than 45 microns.

Soon after the desander, the fluids will go to the second compartment of the mud tank.

Component two) Slurry Dewatering Centrifuge Separation.

The slurry dewatering centrifuge separation unit is a 40 FT containerized system for separation fine solids from the drilling fluids. It consists of following primary gear and device.

2.1) Big Bowl Big Volume Decanter Centrifuge

Model: GNLW553-VFD
Bowl Diameter 550mm(22inch)
Bowl Length 1800mm(71inch)
Max. Capacity 484GPM(110m3/h)
Typical Capacity 400GPM(90m3/h)
Max Bowl Speed 3000RPM
Common Bowl Speed 0~2500RPM
G-Force 1888 @ 2500RPM
Separation point two~5μm
Main Motor 90KW(50HP)
Back Motor 37KW(15HP)
Recommended pump 30 HP
Material: Duplex SS2205 for Bowl and SS316L for Screw Propeller
Screw Protection: Tungsten Alloy Tile Protection
Solids Discharge Port: Interchangeable Tunsten carbide alloy
Handle Panel: Stainless Steel with ABB VFD

The decanter centrifuge has the PLC Control Technique with Touch Screen to manage bowl speed, differential speed, feeding pump speed and flow. Much more more than, the VFD is accessible for handle flucculent pump speed and flow. Password is essential to operate the touch screen. And locking system is offered for operation the touch screen with keys. Flow meters of centrifuge feeding line and flocculent feeding line will send signal to the PLC handle method to avoid the pump from dry suction.

two.2) Double Chamber Flocculation Unit
Model: LR-6000P
Effective Volume: 6000L in two Chamber
Max dry powder 20 Kg/Hr
Feeding by adjustable speed screw conveyor
Material PP
Funnel volume: 30 L
Dimension: 4000 mm X 1500 mm X 1200 mm
If Grow time 30min, for .three% polymer, mixing capacity 6000l/hr 
Energy: 5.0kw, two chamber, with low speed agitator
PLC handle panel, automatic and manually controls feeding screw pump, water pump, motor valves

The approach of the Slurry Dewatering Centrifuge Separation is as below:
The Double Chamber Flocculation Unit will mix chemicals for the flocculation of the drilling mud took from the second compartment . And later on, the slurry and the polymer will be mixed and feed to the large bowl large volume decanter centrifuge.

The VFD decanter centrifuge have G force up to 2000 G, this G force is able to separate the fine solids in the drilling mud and discharge clean water for reuse in the TBM project.

GN Slurry separation plant is widely utilized in the TBM, and horizontal directional drilling and (HDD) mud recycling.

Get in touch with GN Solids America
Tel:+17138780880
Net: http://www.gnsoldisamerica.com
Add:6710 Windfern Road, Houston, TX 77040,USA