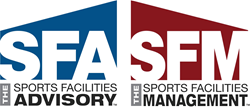
Clearwater, FL (PRWEB) November 12, 2014
Myrtle Beach, SC is the third largest tourism location in America behind Orlando and Las Vegas – its longtime focus on sports is 1 cause the beach town has grow to be so well-liked. John MacDonald, Common Manager of the new Myrtle Beach Sports Center positioned in Myrtle Beach, has announced the signing of 17 event contracts for the new facility, which is scheduled to open in March 2015. “Response has been phenomenal,” says MacDonald. “There are only two weekends still open for the center’s initial six months of operation—Easter and Memorial day.”

Myrtle Beach Sports Center will incorporate one hundred,000 square feet of year-round tournament and events space. The center delivers eight high school basketball courts or 16 volleyball courts with full-length retractable curtains. The courts are also lined so as to be configurable as four collegiate/specialist basketball courts.

“Basketball and volleyball are not the only choices, of course,” says MacDonald. “The center has 70,000 square feet of totally free-span space it is developed to host mat sports, table tennis, pickle ball, trade shows, and numerous other sorts of events.”

When not at the Sports Center, MacDonald notes, athletes and their households will have a host of region activities to select from. These incorporate the Myrtle Beach Boardwalk, named the nation’s number-three boardwalk by National Geographic Household Kingdom Amusement Park, considered the fifth-ideal amusement park in the nation the Huntington Beach and Myrtle Beach State Parks a wide selection of musical entertainment, which includes the Carolina Opry and comprehensive, family-friendly purchasing.1

“This new facility and its locale in one particular of the significant tourist destinations in the U.S.,” says MacDonald, “makes it a have to quit for any occasion owner that wants to give athletic teams with the ultimate in customer service, facilities, value, and guest experience—in and outside of the competition venue.”

Amongst the groups that will be moving their events next year to the Myrtle Beach Sports Center sits the National Travel Basketball Association (NTBA). Says NTBA President John Whitley, “Having the new Myrtle Beach Sports Center permits NTBA to now bring its 1st-class tournaments to a first-class facility. We will be hosting our State and National Championships at the MBSC, and becoming capable to have the games below 1 roof is merely a win-win for all involved, but especially the spectators.”

A essential aspect in the accomplishment of the new Myrtle Beach Sports Center, and of related facilities nationwide, is an explosion of interest in youth and travel sports. “Youth sports tourism wasn’t even a category 4 years ago,” says Dave Hollander, a professor at New York University’s Tisch Center for Hospitality, Tourism, and Sports, “and now it’s the fastest-growing segment in travel. You have got millions of youngsters involved, parents spending thousands of dollars, and cities constructing facilities to host events. It is just massive.”

According to a recent USA Right now survey, at least 35 million youngsters between five and 18 currently play an organized sport every single year in the U.S. Of these, 21 million are involved in non-college youth sports. “I do not see this as trending downward,” says Hollander. “Check out the neighborhood youth sports Television channels in your neighborhood. They are continuing to grow. Cities and towns are seeing advantages as these trips turn into mini-vacations for households, so their incentive to be a player in this is also expanding.”2

Even though the opportunity is real and developing, Dev Pathik, Founder and CEO, Sports Facilities Advisory and Sports Facilities Management, cautions that becoming a player in youth sports demands accurate analysis and planning. Speaking of the Myrtle Beach Sports Center, he says, “The city engaged us to generate a detailed economic forecast and financial effect projections for [Myrtle Beach Sports Center] from the time the project was in its infancy, and then hired our management team, to oversee the pre-opening and day to day operations.”

This cautious and detailed strategy, notes Pathik, is crucial to the success of any new sports facility. “Even with a excellent location and a booming market,” he says, “you have to make particular that what you are doing is precisely calibrated to the marketplace. We recognize this simply because it is our enterprise.”

SFA|SFM works with government entities, economic institutions, private developers, institutional customers, and faith-primarily based organizations to assist them—from the ground up—to optimize the return they make on their investment.

About Sports Facilities Advisory and Sports Facilities Management (SFA|SFM):

The Sports Facilities Advisory and Sports Facilities Management (SFA|SFM) is the leading resource in sports facility arranging and management. SFA|SFM has served a portfolio totaling a lot more than $ 4Billion in planned and operational sports centers in communities throughout the USA and internationally given that its founding in 2003. Youth and amateur sports and neighborhood recreation centers now require professional planning and management. SFA’s proprietary data system—based on years of arranging, funding and managing facilities, coupled with the rise of the youth sports segment—is the engine behind the improvement of SFM. Since its inception, SFM has become an business leader in the management of amateur sports and events complexes, and along with SFA, offers the preparing, financing and management knowledge needed to turn suggestions into profitable recreation facilities. SFA|SFM serves each public and private clientele. Its services fall into four major categories: program, fund, open and handle, which encompass each phase from early stage feasibility studies to preparing financing documents, overseeing development and opening and complete-time management solutions. SFA|SFM’s achievement depends upon its mission to dramatically increase communities by way of the opening or optimization of sports and recreation centers. For a lot more info, pay a visit to http://www.sportadvisory.com/home.html.

1. “List of Attractions in Myrtle Beach, South Carolina,” Wikipedia, en.wikipedia.org/wiki/List_of_attractions_in_Myrtle_Beach,_South_Carolina

2. Koba, Mark, “Spending big on kids’ sports? You’re not alone” CNBC, January 13, 2014. cnbc.com/id/101326773#.





Locate A lot more Precision Engineering Services Press Releases