A couple of nice milling engineering photos I found:
PA – Mill Run: Fallingwater – Dressing Area
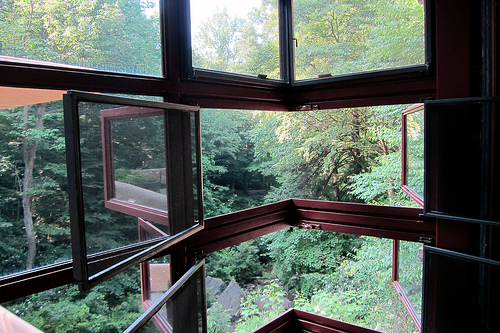
Image by wallyg
Fallingwater functions a 3-story light tower or light screen, which runs through the Dressing Space or Edgar Kaufmann Sr’s Study on the second floor, and Edgar Kaufmann Jr.’s Study on the third floor. At the corner, the casement windows open outward, breaking the down the box and permitting the corner to vanish. At Edgar Kaufmann Sr.’s suggestion, exactly where the windows meet the ragged stones walls, the glass runs directly into caulking channels, blurring the line between the exterior and interior space. When viewed from the exterior, the vertical shaft of glass serves to balance the structural stone masses and preserve the house’s transparency. The ceiling is treated with a bevel, minimizing the cantilevered mass of concrete, steel and stone to a practically invisible sliver exactly where it meets the window frame.
Fallingwater, sometimes referred to as the Edgar J. Kaufmann Sr. Residence or just the Kaufmann Residence, positioned inside a five,100-acre nature reserve 50 miles southeast of Pittsburgh, was designed by Frank Lloyd Wright and built in between 1936 and 1939. Constructed over a 30-foot flowing waterfall on Bear Run in the Mill Run section of Stewart Township, Fayette County, Pennsylvania, the property served as a trip retreat for the Kaufmann family members including patriarch, Edgar Kaufmann Sr., was a effective Pittsburgh businessman and president of Kaufmann’s Department Shop, and his son, Edgar Kaufmann, Jr., who studied architecture briefly below Wright. Wright collaborated with employees engineers Mendel Glickman and William Wesley Peters on the structural design and style, and assigned his apprentice, Robert Mosher, as his permanent on-site representative all through construction. Regardless of frequent conflicts amongst Wright, Kaufmann, and the building contractor, the home and guesthouse had been finally constructed at a price of 5,000.
Fallingwater was designated a National Historic Landmark in 1966. It was listed among the Smithsonian’s 28 Areas to See Prior to You Die. In a 1991 poll of members of the American Institute of Architects (AIA), it was voted "the ideal all-time function of American architecture." In 2007, Fallingwater was ranked #29 on the AIA 150 America’s Favourite Architecture list.
National Register #74001781 (1974)
Sobey Manufacturing shingle mill, 1915

Image by Seattle Municipal Archives
Item 51879, Engineering Department Photographic Negatives (Record Series 2613-07), Seattle Municipal Archives.
7-Axis Milling Equipment (NASA, Marshall Center)
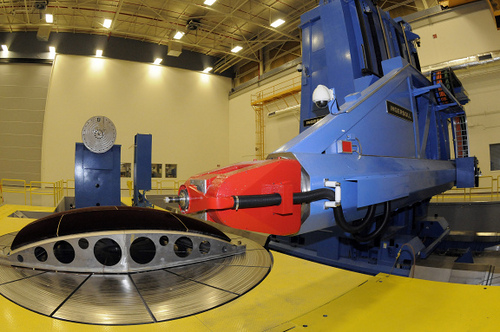
Image by NASA’s Marshall Space Flight Center
Editor’s Note: This image is one of a series showing engineering technology at NASA’s Marshall Space Flight Center in Huntsville, Ala.
Caption: Ares 7-axis milling gear and facilities.
Credit: NASA/MSFC/D. Stoffer