A couple of good custom metal parts photos I found:
Morgan +4

Image by pedrosimoes7
Av. de Roma, Lisbon, Portugal
in Wikipedia
1952 "flat radiator" Morgan +4
1963 Morgan +4
The Morgan +four was introduced in 1950 as a larger-engined ("plus") automobile than the 4–4. The +4 used the 2088 cc Normal Vanguard engine, although the 4–4 utilised a Common Particular 1267 cc engine (1950–58). Later +4s utilized Triumph TR2–TR4 engines (1954–1969). +four production was suspended in 1969 but brought back in 1985 with a Fiat engine (1985–1988) and then a 4-cylinder Rover engine (1988–2000). Production was once more suspended and the Plus 4 returned once much more in 2004 with a 155 bhp (116 kW 157 PS) Ford 4-cylinder.
+four+ .
Morgan +four+
A version of the +4, designated the +four+, was created from 1964 to 1967 with a modern fibreglass coupe body. The light weight and lowered drag qualities enhanced the overall performance of the +four+ over the normal +four in every single aspect. Nevertheless, the traditional Morgan enthusiasts did not embrace this departure from Morgan custom, and mainstream enthusiasts did not embrace the seemingly archaic +4 chassis. Only 26 +4+ cars were built.
Morgan four/4 [edit]
1974 Morgan 4/four
The 4–4 was replaced by the four/4 in 1955. The 4/4 now utilizes the +eight chassis and a Ford engine.
Morgan +eight [edit]
Faced with the decreasing availability of big 4-cylinder engines for use in their +4 models, Morgan started to set up the not too long ago accessible Rover V8 engine in their automobiles in 1968, providing these cars the model designation "+eight".
The engine displacement jumped from the two.3 L of the Triumph TR4 engine to 3.5 L, then 3.9 L (1990), 4. (1998–2004) with an optional four.6L (1996–2000) all primarily based on the very same Land Rover block. However, the V-8 was no longer than the Triumph. These attributes created the +eight accelerate significantly far more quickly than the early +four and also enhanced its road-holding capability.
Horsepower (143–204 bhp), weight and efficiency varied with emission and structural laws through its history. In its final type, the GEMS Land Rover V8 made 190 hp (140 kW). Thus powered, the vehicle could accelerate from 0–60 mph in five.6 seconds.
Roadster at 76e international Motorshow Geneva 2006
Roadster
In 2004, Morgan came out with a standard styled model to replace the departing Plus 8. The new model, named the "Roadster" was powered by a Ford UK Mondeo V6 creating 204 bhp (152 kW 207 PS). In 2007, the Mondeo engine was replaced by a US version of the same engine in the Roadster II. In 2011/2, the engine was again replaced by the 3,7 Duratec Cyclone engine and bhp increased to 280. The firm calls this latest Roadster version the Roadster 3.7.
Morgan Aero eight (Series I-IV) [edit]
A Contemporary Morgan Aero eight at the Scarsdale Concours
In 2000, the Morgan Aero eight was introduced and, as always, the wooden physique substructure was ash. (Contrary to common myth, nevertheless, the chassis is metal aluminium for the Aero 8). The Aero eight, with a BMW V8 engine in a auto weighing less than a BMW Z4 and considerably much less than a BMW M3, (though more than conventional Morgans) is even more quickly than the Plus 8, delivering what Autoweek magazine termed supercar functionality. The newest Aero eight (Ser. IV) puts out 367 hp (274 kW) at 6100 rpm providing it a top speed of more than 170 mph (270 km/h). Due to the Aero 8’s light weight it can do 0–62 mph (one hundred km/h) in four.five seconds.[7]
In the course of its client production lifetime (2002–2009), the Aero was configured in 5 official versions, (I,II, III, IV and the Aero America) with variations in styling, engines, transmissions, braking and suspension. The Company canceled its production in 2009. It was followed by the Aeromax, a limited coupe edition of 100 units produced in between 2008 and early 2010.
The year of highest production was 2002.
Morgan Aero 8
The Morgan Aeromax is a coupé variation of the Aero 8 commissioned for Prince Eric Sturdza, President of Banque Baring Brothers Sturdza SA.[eight] Production restricted to one hundred automobiles was later authorised by Sturdza, every promoting for £110,000. Consumers have integrated Richard Hammond, Rowan Atkinson, and Paul O’Grady.
Morgan Aero 8
The Morgan Aero SuperSports is a targa-roofed version of the AeroMax, sharing its bonded aluminium chassis and reduced bodywork with the coupe.[9] It was launched at the 2009 Pebble Beach auto show in California.
Morgan Aero Coupe [edit]
Principal post: Morgan Aero 8
The Morgan Aero Coupe is a challenging prime version of the Aero SuperSports, sharing its bonded aluminium chassis, bodywork, suspension, and engine. It was launched at the end of 2011. It was not accessible in the USA.
Morgan Aero Plus 8
Primary report: Morgan Aero eight
The new Morgan Aero Plus eight is a classic physique version of the Aero SuperSports and Aero Coupe, sharing their bonded aluminum chassis, bodywork, suspension, and engine. It was launched at the finish of 2011. It was not accessible in the USA.
Morgan Eva GT
Principal article: Morgan Eva GT
Based on the same chassis as the Aero Supersports, the Eva GT will be a two+2 grand tourer, and as such it is longer in the physique. The Eva GT will use BMW N54 twin-turbo straight-6 producing 302 bhp, this is Euro-6 emissions compliant. Shown at Pebble Beach in clay in 2010 and expected to go on sale in 2012, deposits have been taken considering that 2010. At the end of 2011, Morgan announced that it will use new magnesium technologies for the physique and consequently it will not be re-presented till 2014 with deliveries right after that.
2011 Morgan Threewheeler
Morgan three Wheeler[ten]
The Morgan Motor Organization announced that they would launch the ‘3 Wheeler’ in 2011[12][13][14][15] at the Geneva Motor Show.[13][14] The Threewheeler was initially said to have a Harley-Davidson Screaming Eagle V-twin engine and a Mazda 5-speed manual transmission,[12][13][14][15][16] and was estimated to deliver 115 horsepower (86 kW)[12][14][15][16] at the rear wheel.[15][16] Nevertheless, there was a surprise when the prototype that was shown at Geneva had a S&S engine. Production 3-wheelers turned out to have S&S engines.[17][18] The kerb weight was initially estimated to be less than 500 kilograms (1,102 lb),[12][13][14][16] but the final weight was tested at 550 kg. The acceleration from zero to 60 miles per hour (97 km/h) was estimated by Morgan to occur in four.5 seconds, with an (est.) top speed of 115 miles per hour (185 km/h).[12][13][14][15][16] The three-wheeler is to be homologated as a motorcycle in the United States.[12][16] The organization states that 850 deposits have been taken considering that the announcement in 2011. Buyer deliveries began in Europe in February 2012. USA deliveries are not anticipated before June 2012, when the first imported three-wheeler was displayed in New York City and at the Greenwich Concours d’Elegance. The Morgan Threewheeler was featured in a Series 18 episode of UK motoring show Best Gear exactly where presenter Richard Hammond picked the Morgan Threewheeler in a comparison of track-day vehicles. The Threewheeler won the "Not-A-Vehicle of the Year 2011" in Leading Gear (magazine).
Availability to the United States.
Morgan Motor factory, principal entrance
For element of the 1950s and 1960s, the USA offered the organization with its biggest marketplace worldwide, taking up to 85% of all production.[19] This ended with the very first wave of US security and emission regulations in 1971. For several years (1974 to 1992), all Morgans imported into the United States were converted to run on propane as fuel to pass the U.S. emissions regulations. Nevertheless, this conversion, along with bringing the cars into compliance with US car security leglislation, was carried out by the dealership, and not by the factory, making the automobiles grey industry automobiles.
Even so, when the Rover Group re-certified their V8 engine for use in the Range Rover 4×4 sold in the U.S., Morgan was able to use the same engine for a fully US compliant stock Morgan from 1992 to 1996,[citation needed] and once more from 1998 to 2004.[citation needed] In 2005, the engine was replaced with the US version of one more traditionally shaped model (with a V6) known as the Roadster.
In 2002, Morgan centralised its international compliancy development and regulatory interaction in-property.[citation needed] In 2005, its correct to import its classic models ceased when supplies of its required airbag had been exhausted and no replacement was developed. In 2006, a request for an airbag exemption to the U.S. National Highway Traffic Safety Administration was refused, and the import of classic Morgans ceased.
In 2005, the new Morgan Aero eight model (versions two and 3) received a 3 year exemption from rear impact non-compliance,[22] along with a separate exemption for compliance with "advanced airbag requirements".[23] The rear-influence exemption lapsed in May possibly 2008 without further application. Morgan has indicated to its US dealers that it plans to re-apply for US certification for some model at as yet an undetermined date in the future.[citation needed]
In April 2012, the new Morgan three Wheeler was show-cased at the New York International Auto Show, at the Jacob Javits Center, by Bobby Singh and Gideon Lang-Laddie of Manhattan Motorsports www.morgan3w.com. This was the 1st time in ten years that Morgan had had a presence at the largest of the American automobile shows and was the 1st US specification Morgan three Wheeler in the USA. The Morgan 3 Wheeler was voted one of the "Hottest Cars Of The Show" by G4TV.
In May possibly 2012. Manhattan Motorsports took delivery of Charles Morgan’s Superdry edition Morgan three Wheeler and ready it for its first main American trial. This car was driven across the States, from New York to Los Angeles by Charles Morgan and his wife,covering 3000 miles, in the Gumball 3000 Rally. At the end of the 7 day drive, the Morgan 3 Wheeler was awarded the "Spirit of Gumball" prize.
Basic traits [edit]
Conventional Morgan sliding kingpin suspension
In spite of their standard style, Morgans have constantly had sporting or "sports car" functionality, due to their extremely low weight.
Among their enthusiasts, Morgans are affectionately recognized as "Moggies".
H.F.S. Morgan’s 1909 Runabout utilized sliding pillar suspension, an independent front suspension system with every front wheel mounted on a kingpin mounted to slide along a fixed pillar and located by a spring. Morgan used developments of this suspension system throughout its existence and it is still used on Morgan’s "classic" line, although not on the Aero eight or its derivatives.
BROTHERS 14th Annual Chevy & GMC Truck Show
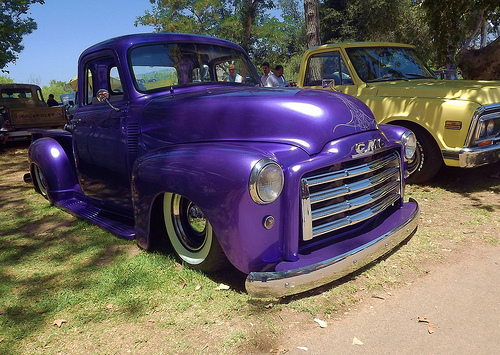
Image by ATOMIC Hot Links
Custom Portion for Thule Rack
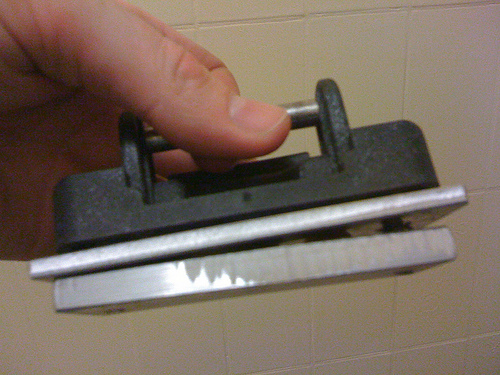
Image by acodring
Thule does not make components to attach their roof system to a Traverse so I had these custom made locally at Johnson Welding Works on Beech St. Bob is great to operate with and has helped me with a few modest jobs over the years.