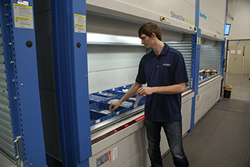
Westbrook, ME (PRWEB) October 15, 2014
FlightSafety International is the world’s major provider of aviation coaching and manufacturer of full flight simulators, visual systems and displays. With a lot more than 40 Finding out Centers, worldwide, 1,800 instructors, 3,000 courses on 135 aircraft sorts, FlightSafety International supplies more than a million hours of coaching every year on a wide selection of aircraft types from fixed wing to helicopters, utilized in corporate aviation, by industrial airlines, and government and military agencies. Making use of more than 300 simulators to train clients in more than 167 nations, FlightSafety International has a single mission: Safety.

The Broken Arrow, OK manufacturing facility was moved to a new 375,000 square foot facility within the very same city limits. This new facility permitted FlightSafety International to improve efficiencies and expand capabilities. With the capacity to produce up to 19 simulators at when, the stockroom keeps busy filling orders for the production line.

Component parts are picked on a every day basis and sent to kitting exactly where the kits are stored until manufacturing is prepared. With demand on the rise, the stockroom necessary a more efficient and controlled environment. “Component components and kits were stored in cardboard boxes on shelving, producing order fulfillment a time consuming, labor intensive method and inventory susceptible to shrinkage,” says Mike Halsey, Director of Manufacturing and Material Management. The move to the new facility was the best chance to boost the stockroom.

An Automated Solution 
The installation of four, 36’ tall Shuttle XP Vertical Lift Modules (VLMs) decreased the footprint of the element and kitting regions in the new facility from roughly 6,454 square feet to 960 square feet, an 85% floor space savings! The VLMs are used in two work zones. The 1st zone utilizes two of the VLMs for element parts. Integrated with pick to light technologies, inventory management software program and a ten position batch station to increase productivity and boost inventory handle. The second zone utilizes the other two VLMs integrated with pick to light technology and a ten position batch station as buffer storage for kitting.

Inventory Manage Reaches New Heights
Previously with the shelving program, there was limitless access to inventory. This area was not safe and without having inventory personnel obtainable after hours to monitor components movement, inventory parts would come up missing, making an untraceable loss in inventory. “After implementing the Shuttle VLMs, inventory is significantly far more correct,” says Halsey, “The VLM operators are given access to the machine, but every single transaction is now monitored and recorded electronically in the inventory management software.”

Less Labor
The old shelving technique required seven individuals in the elements location and seven men and women in the kitting area. Because installing the Shuttle VLMs, only a single particular person is required in the components location and a single individual in the kitting location. With labor reduced by 86%, other workers have been reassigned to distinct areas of the warehouse to increase efficiencies. Even though the two workers that remain in the Shuttle VLM region are selecting and kitting for the majority of the day, time is also spent working on other tasks such as inventory counts and replenishment orders. “Time spent walking and searching for components and kits has been eliminated, enabling our employees to commit time on other critical tasks such as replenishment,” says Gene Harvey, Inventory Manage Supervisor.

Accuracy Takes Off
A principal catalyst for implementing the Shuttle VLMs was the potential to enhance accuracy. “The opportunity for human error was affecting our pick accuracy and impacting manufacturing,” says Harvey. In the occasion of a mispicked portion, not only did the incorrect part make it to the manufacturing floor in the 1st spot, that portion required to be received back into the shelving location whilst the new portion was picked and delivered to the production line. Further, the incorrect component was typically left on the shop floor for fairly a whilst till it was ultimately returned. “When the incorrect part makes it to manufacturing, it utilized to result in a shutdown – with the VLMs that doesn’t happen now,” says Harvey.

With the Shuttle VLMs, there is restricted to no opportunity for error. Integrated with choose to light technology, the Transaction Info Center (TIC) directs the operator throughout the selecting processing. “Accuracy is at 99.9% – up from the mid 90%’s,” says Harvey.

Old Methods Are Cancelled
Previously, all component components had been stored on shelving and in cardboard boxes. “The amount of travel time 1 particular person would commit walking and searching for a component was time wasted,” says Harvey. A paper pick ticket would inform the pickers what parts to choose for each order. The workers would walk the entire warehouse to gather components for the order. After all of the parts had been picked the order would be delivered to the kitting area.

The kitting area would receive the order and store it as a kit in buffer storage shelving. Upon production request, kits would be pulled and assembled and then sent to production. In this manual process, components were touched and moved a number of occasions before they created it to the production line, leading to inefficiencies.

VLMs Speed Processes
Components Zone
Just over 8,000 SKUs were moved from the old shelving region into the two new Shuttle VLMs dedicated to component components. The other two VLMs were committed to buffer storage for kits. “There is now a continuous flow from the component components to kitting and down to production,” says Halsey.

The organizing department generates orders in the MRP technique. The orders are then sent to the inventory management software. After the orders are loaded, the picker in the component region can start off filling orders. Picking priority is primarily based on the kit due date therefore the most urgent kits are picked initial.

There is a 10 position batch station positioned subsequent to the Shuttle VLMs allowing the operator to pick up to 10 orders at a time. The operator selects up to 10 orders and assigns a tote on the batch station to each and every individual order, and then with the touch of a button the picking method starts. The inventory management application tells the Shuttle VLM which element demands to be picked, pulling the proper tray from the machine. The tray is delivered through an extractor that runs up and down the middle of the unit. Delivered to an ergonomic height, the TIC lights direct the operator to the proper component location, displays the part number and the quantity to pick. As soon as the 1st part in the order is picked, the operator confirms the choose with a process comprehensive button, or with the VLM confirmation bar. A bar coded label is printed and the operator bags and tags the portion for movement down the conveyor to the kitting VLMs. This supplies good identification of material throughout the complete method and ensures the proper component has been picked and kitted.

Every single position on the batch station is fitted with a place light that directs the operator in which orders to place the parts picked from the VLM. While the operator distributes the components among the orders in the batch, the VLM is delivering the subsequent element to the access opening, eliminating wait time and maximizing productivity. As orders are completed they are sent to kitting through conveyor.

Kitting Zone
Upon arrival at kitting, the operator bar code scans every tote, placed at one particular of the ten batch light positions, and the VLMs presents a tray and uses the TIC to direct the operator to the exact location on the tray to retailer the kit. The kit can remain in the VLM buffer storage for up to 60-90 days. The production floor sends a request to kitting to pull the appropriate kit quantity and the operator retrieves the kit requested from the Shuttle VLM and delivers it to manufacturing.

“The machines are hugely reputable with practically % downtime. The service team has an superb response time when we’ve required it,” says Halsey.

Leaning Out Waste
The earlier shelving system was not effective sources have been becoming wasted to total day-to-day tasks. “Valuable time and manpower was wasted in the previous method, eliminating that waste was portion of the justification for this project,” says Halsey.

Maintaining Up With Demand

The Shuttle VLMs have enhanced stockroom processes and efficiencies, saving time and increasing inventory accuracy. “In order to meet the demand on the shop floor, we would have had to add more people – we couldn’t have kept up otherwise. The Shuttle VLMs solved that difficulty and allowed us to enhance productivity,” says Harvey.

Kardex Remstar, LLC, a firm of the Kardex Group is a leading provider of automated storage and retrieval systems for manufacturing, distribution, warehousing, offices and institutions. For details about our dynamic storage solutions, contact 800-639-5805 or pay a visit to http://www.kardexremstar.com.





Much more Machined Components Makers Press Releases