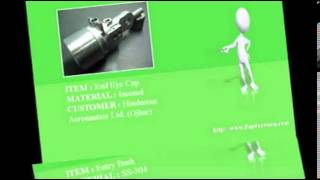
http://paprecision.com/ The causes why cutting feed In addition to speed can be worthwhile of precision machining for parts? Precisely how a lot part of the co…
Video Rating: / five
Rapid Prototyping China
http://paprecision.com/ The causes why cutting feed In addition to speed can be worthwhile of precision machining for parts? Precisely how a lot part of the co…
Video Rating: / five
A couple of nice precision machined element pictures I discovered:
Touring Numet Machining Tactics, Inc. in Orange
Image by CT Senate Democrats
State Senator Gayle S. Slossberg tours Numet Machining Strategies in Orange with Joseph Sartori, Numet’s Vice President of Operations. Numet is a manufacturer of precision machined elements, and was in a position to develop and retain jobs thanks to its participation in Connecticut’s Modest Enterprise Express Program and the Connecticut Insurance coverage Reinvestment Fund. (October two, 2013)
Vasteras, Sweden (PRWEB) September 09, 2014
As the schedule ramps up to production of the COMAC 919, two very first-tier Chinese suppliers have bought fluid cell presses from Avure Technologies to decrease fabrication steps and drastically decrease the price of components they are manufacturing for the new single-aisle aircraft.

Shanghai Aircraft Manufacturing Co. Ltd. and Xizi Aviation will set up the sheet metal forming presses in facilities at Shanghai and Zehjiang, China, respectively.

Shanghai Aircraft has chosen an advanced 68,000-ton fluid cell press, with a forming location of 1.4 x 4 m (55.1 x 157.5 inch), to extend its current capacity. Making use of ultra-high stress to type a wide range of complicated shapes, Avure Flexform™ fluid cell presses are a expense-effective, versatile manufacturing remedy, specifically when speed is vital in reducing time-to-industry and maintaining global competitiveness. The new Avure program is being designed for 1000 bar stress, a great asset when streamlining production to decrease the need to have for manual labor.

Xizi Aviation, a relative newcomer in the aerospace fabrication loved ones, chosen Avure’s recently introduced model, the QFC .7×1.8-800, a 17,000-ton fluid cell press with a table size of .7 x 1.8 m (27.6 x 72 inch) and designed for 800 bar pressure. With a rapidly, 60-second procedure cycle, combined with low operating fees, a space-saving little footprint, and straightforward installation directly at floor level, this press is a ideal match for Xizi’s concentrate on fabricating sheet metal parts for the airframe structure.

“These state-of-the-art higher-stress fluid cell presses are effectively suited to meet today’s imperative for much less and much less labor involvement, enabling the COMAC effort to compete with Western aircraft manufacturing approaches,” comments Sture Olsson, Avure’s Worldwide Metal Forming Enterprise Unit Director. “The introduction and mixture of higher-pressure, modern day tool design, and cautious fabrication logistics might decrease earlier essential fabrication steps by as a lot as 50 %, doubling the production capacity and cutting price by as much as 80 %.”

With 156 to 168 seats, the new C919 is a new short/medium variety commercial jetliner aimed at meeting increasing airline interest worldwide in single-aisle models. It is made to compete with the Airbus A320-NEO and the Boeing 737-MAX. All new aircraft styles seek to increase fuel efficiency, improve safety, enhance passenger comfort, and increase manufacturing efficiencies.

The new Flexform press will turn into Shanghai Aircraft’s second fluid cell press its first was supplied by Avure (formerly under the brand name ASEA, then ABB) nearly 30 years ago, and is nevertheless operational at complete processing parameters nowadays.

Avure will be exhibiting at EuroBLECH 2014 in Hannover, Germany, October 21-25, in Hall 17, Stand D122.

About Avure Technologies 
An innovator with a powerful record of accomplishment, Avure Technologies (formerly recognized as ASEA, ABB, and Flow) demonstrates its knowledge in higher stress by occupying leadership positions in industrial and food applications. The business is the biggest worldwide provider of ultra-high pressure systems utilized to kind sheet metal, to process sophisticated materials, and to pasteurize foods without heat or chemical substances.

Avure has installed more than 1,700 high-pressure systems worldwide, more than all other competitors combined. These systems are characterized by technically sound design, superior reliability, energy efficiency, low maintenance expenses, and numerous years of encounter. Several Avure presses have been in service for more than 40 years, and some have surpassed 1 million higher-stress processing cycles.

Avure Industrial Group headquarters in Västerås, Sweden, home equipment style, manufacturing, and support operations, with additional facilities in Columbus, Ohio, USA, and regional sales and assistance operations globally. Read much more about Avure Technologies: http://sector.avure.com/goods/fluid-cell-presses-rectangular-forming-trays

About Shanghai Aircraft 
Founded in 1950 and primarily based in Shanghai, China, Shanghai Aircraft Manufacturing Co., Ltd. manufactures and assembles aircraft components and elements, such as the horizontal stabilizers it produces for Boeing 737 aircraft. The business also supplies study and improvement and repair for massive industrial aircraft. It operates as a subsidiary of Commercial Aircraft Corporation of China, Ltd. Study a lot more about Shanghai Aircraft at http://english.comac.cc/

About Xizi Aviation
With its facility in Zhejiang, China, established in 2010, Xizi Aviation is a tier-1 supplier of the C919 aircraft airframe structure, also providing high-good quality merchandise and solutions for Airbus, Boeing, COMAC, AVIC, Cessna, Bombardier, and other individuals. Xizi Aviation capabilities extend from CNC machining, composite structures forming, and sheet metal forming, to heat and surface remedy, component assembly, digital measurement, and NDT. The business is a essential company sector of Xizi UHC, which contains three subsidiaries: Zhejiang Xizi Aviation Sector Co., Ltd., Shenyang Xizi Aviation Industry Co., Ltd., and Zhejiang Xizi Aerospace Fasteners Co., Ltd. Study more about Xizi Aviation at http://en.xiziac.com/





Mike O’Connell from ATL (Ad Tape & Label) in Menomonee Falls, Wisconsin, discusses disposable healthcare and safety label capabilities and services.
Video Rating: 5 / 5
Russia's Putin promises new weapons to fend Western threats
With hundreds of subcontractors going out of production, Russian arms companies typically had to make components themselves, swelling expenses and affecting production top quality. The difficulties faced by the Russian arms … Talking about prospective threats …
Study much more on The Spokesman Overview
NN, Inc. Announces Two Senior Level Appointments Following Completion Of …
NN, Inc. companies and supplies higher precision metal bearing components, industrial plastic and rubber products and precision metal components to a selection of markets on a international basis. Headquartered in Johnson City, Tennessee, NN has 25 …
Study far more on CNNMoney
Welcome to Hindustan Unity Engineering, Manufacturer and Supplier of Precision Turned Component and Parts. We are an ISO 9001:2008 certified firm, establi…
Video Rating: / five
A handful of nice precision element makers photos I found:
Apollo 14 Docking Ring
Image by jurvetson
Milled from a solid block of titanium, with twelve docking latches, it is a marvel of precision design and style in the era ahead of CAD/CAM.
The Smithsonian believed this was the CM docking ring from Apollo 14 Command Module, and had paperwork to help that. I feel it is the sister unit, a big structural engineering element utilised for ground testing to try to recreate the series of docking failures seasoned early in the Apollo 14 mission with the probe that was brought back (normally the docking probe would be left behind). Hence the Apollo 14 label on the base and description at the Bonhams’ auction:
NASA’s choice to fly Apollo missions employing a lunar orbit rendezvous approach necessary the improvement of a method to join, separate, then rejoin two spacecraft. This system also had to let astronauts to move internally between the Command and Lunar Modules. The flight configuration selected was an effect system consisting of a probe situated at the forward end of the Command Module (CM) and a funnel-kind drogue located at the prime of the Lunar Module (LM). The CM’s probe was mounted to the docking ring, which provided a point of structural integrity for the two docked cars as soon as the probe was removed. Removal of the probe produced a tunnel so the crew could travel between the docked cars. A series of latches about the docking ring locked the cars collectively. The tip of the probe had a set of 3 modest capture latches which had been developed to hold the vehicles with each other lengthy adequate that the bigger docking ring latches could be engaged.
Just right after the Saturn V’s third stage sent Apollo 14 on its planned trajectory toward the moon, Shepard along with astronauts Edgar Mitchell and Stuart Roosa seasoned difficulty docking the CSM to the LM. 5 attempts were created but the docking probe capture latches never engaged to secure the two cars together. This could have scrubbed for the second time in a row a lunar landing mission. With the failure of Apollo 13 due to a Service Module oxygen tank explosion, a scrub of the Apollo 14 lunar landing would most definitely have offered ammunition to these in Congress lobbying for an early termination of the Apollo Plan.
Soon after practically two hours of delays and on the sixth try, with Roosa holding the CSM tight with the LM for many seconds, the latches lastly engaged. The crew then activated the series of larger latches mounted along the docking ring to receive a "hard dock" configuration. Though they had been ultimately docked, Mission Manage and the crew’s concern shifted to the possibility that the program could fail when it was most necessary, the redocking of the LM Ascent Stage following Shepard and Mitchell’s return from the moon. If this happened the crew could be forced into performing a space walk in order to return to the CSM. The lunar rocks and scientific data may well have to be abandoned in the LM pending the precise situations of a possible lunar orbit docking problem. The probe was completely inspected by the crew throughout the coast period to the moon and they sent detailed verbal descriptions plus television pictures to Mission Control. Because the probe now showed standard operation of the capture mechanism, NASA created the selection to proceed with the planned mission.
The redocking while in lunar orbit was fully normal. The docking probe (usually jettisoned with the LM) was returned to earth for inspection and evaluation.
NASA and spacecraft manufacturer North American Rockwell performed an exhaustive series of tests to the docking system. All elements (probe, latches, docking ring) had been tested "in location" with the recovered Apollo 14 CM, then each was removed for a series of combined and person tests. The docking method dilemma was a major reason the docking ring was removed and never ever re-installed into the Apollo 14 CM. Post-flight evaluation of tv, motion image film, accelerometer info, and reaction control system thruster activity indicated that probe-to-drogue get in touch with conditions were as expected for all docking attempts. The probe’s capture latches should have worked on every of the 1st 5 docking attempts. A plunger-variety component in the capture latch failed to reach a forward or locked position most likely due to some kind of foreign debris or contamination. A change in the size of the plunger due to temperature was an added possibility. Internal harm to the capture-latch mechanism was ruled out as the cause because the program functioned correctly in all subsequent operations following the sixth docking try and throughout post flight testing. The debris or contamination most probably became dislodged following the fifth docking try, enabling the system to operate effectively from that point. NASA and Rockwell created the decision to supply a protective cover on the tip of the probe to prevent contamination during future flights.
Throughout the tests, the ring was shipped between a variety of NASA and contractor facilities through a 39 by 39 by 12 inch wood transit case which is integrated with the ring. The ring itself has a series of inspection stamps and ID numbers that study: "MDR 408699, V36-316250-9, 06361-B009522, MR 361588, DEC 9 1968, V36 316250 31, ASSEM, FEB 18 1969, 06361A015194." A separate 6 by 3 inch yellow "Temporary Parts Removal Tag" repeats many of these numbers and has the added hand-written information of: "TPS 112, REM #103, Docking Ring, S/C 110, 2/14/72."
Included are copies of documents listing the NASA artifact number (2243) getting from Command Module (S/C # 110) for the transfer to the National Air and Space Museum (NASM) and deascession papers from NASM.
The Apollo 14 docking ring is the single biggest and heaviest piece of lunar spacecraft structural gear ever to be provided to private hands. The flown CM docking ring, the twin of this one particular, remained with the ascent stage of the Lunar Module Antares when it was jettisoned. Antares was then deliberately crashed into the moon’s surface to simulate a "moonquake."
For expertly crafted, precision engineered sheet metal manufacture and metal turned components, you want Dynamica Ltd. Call us these days to talk about your requirem…
Video Rating: / five
How to neck turn brass. It really is a fairlt straightforward process but it should be accomplished proper. If the case neck is too thin the neck will prematurely split. If you happen to be conve…
Video Rating: 4 / five
http://www.paprecision.com/ Cutting Speed and Feed – Its significance in Precision Machining of the metal elements The term ” cutting speed, ” as applied t…